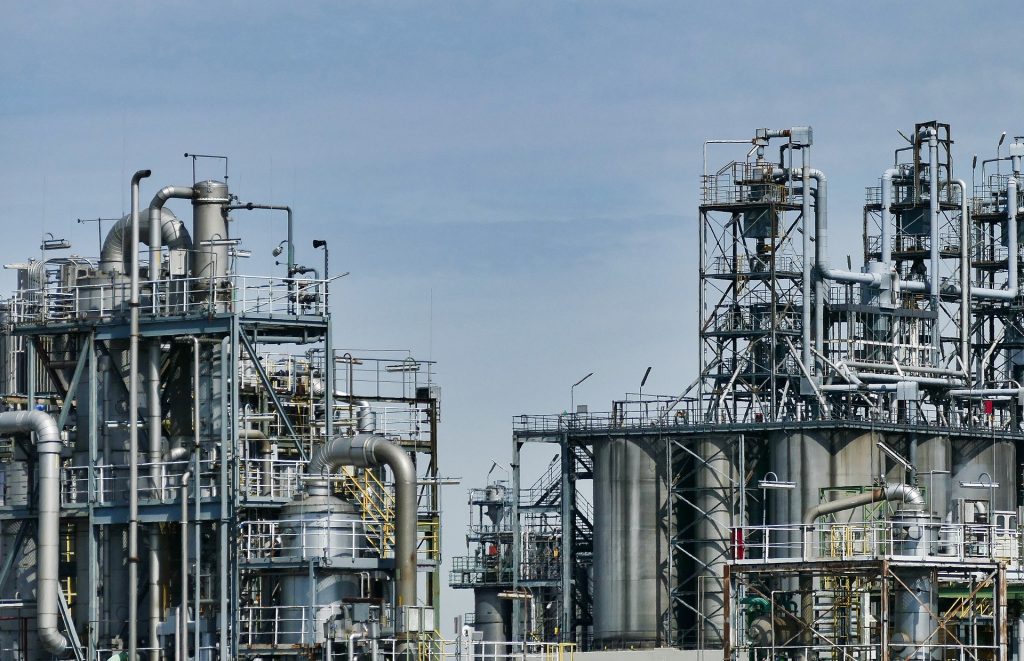
HOIS Highlights 2023-2024
Effective Heat Exchanger Tube Inspection
Background
Heat exchangers and condensers are widely used in oil and gas processing and are designed to maintain 100% separation between the products in the tube (tube side) and the products in the vessel (shell side). A leaking or damaged tube can result in significant loss of production and can cause environmental issues and there is also potential for loss of life. Tube failures are one of the biggest contributors to unplanned downtime and therefore optimised inspection offers the opportunity to significantly improve operational reliability.
As a result, HOIS conducted an extensive programme of blind trials of NDT methods to detect and characterise indications that can be present on the external and internal surfaces of heat exchanger tubes.
The scope for this project covered plain and integral finned carbon steel tubes and plain low alloy steel tubes.
A mixture of both ex-service heat exchanger tubes with service-induced damage, and manufactured tubes with machined flaws were assembled. For the manufactured tube samples, the defect types present were isolated pits, pitting clusters, general corrosion, erosion, and fretting. The tubes were accurately benchmarked using a combination of UT and mechanical measurement.
Trials were conducted using the following techniques: IRIS, Remote Field Testing, Remote Field Testing Array, Magnetic Flux Leakage, Near Field Array, Partially Saturated Eddy Current and Boroscopy. The trial participants were Baugh & Weedon, CAN, Delta Test, ETherNDE, Oceaneering, Waygate Technologies, Versa Integrity and Eddyfi.
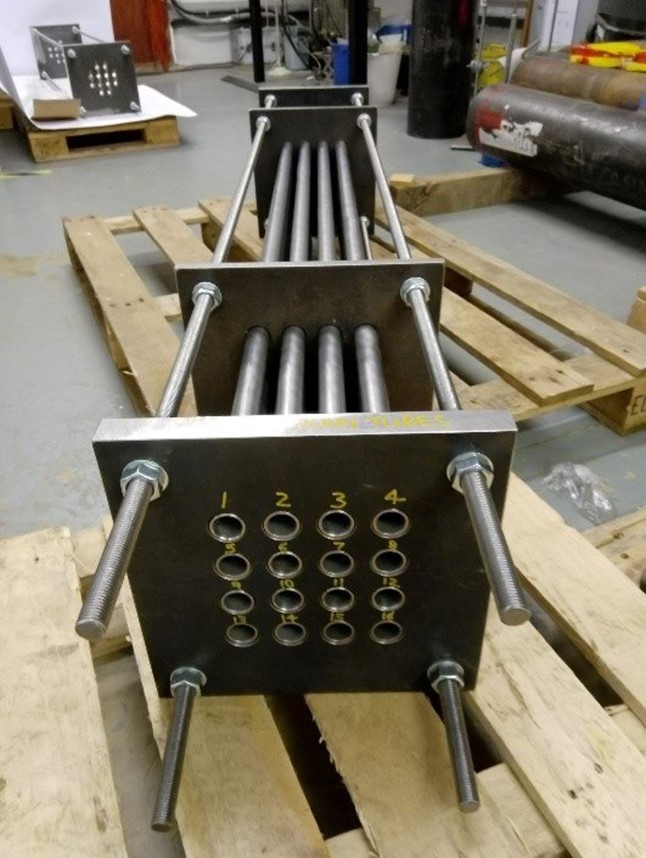
Progress Update
The final trial using Remote Field Testing Array was conducted by Eddyfi.
The trial report detailing the performance of all techniques has been completed and is confidential to HOIS members.
This project is complete.